Welding Underwater – Engineering Report
- To find inspiration for your paper and overcome writer’s block
- As a source of information (ensure proper referencing)
- As a template for you assignment

Introduction
Reference list.
Welding is a process of combining two metal parts through selected heating procedures (Welding, 2012). Here, two metal parts combine to form a permanent bond after cooling (Welding, 2012). The design of multiple structures, machines, and many engineering products depend heavily on welding processes. In an effort to develop welding approaches that align with different needs in engineering practice, engineers develop a range of welding products (Welding, 2012). Such a direction provides engineers with an array of welding products that can suit unique applications in engineering.
The need to install and use several engineering products in water habitats makes it necessary to do welding operations underwater (Lythall, 2000). Under-water welding is a product of years of research on necessary adjustments needed to carry out under-water welding. The United Arab Emirates ranks high among areas with high under-water welding activities.
Emerging offshore infrastructures, such as offshore oil wells, profile the UAE as a high market for under-water welding (Keats, 2011). To deal with the many challenges that come with installing, or repair of the high number of offshore structures that emerge in the UAE, professionals who work in repairing and installing multiple offshore structures must acquire requisite training in under-water welding.
There are two types of underwater welding: dry and wet welding (Vijay, 2011). Dry welding employs a chamber to seal the area that needs welding repair (Lythall, 2000). The chamber must have requisite components, such as oxygen (incorrect concentration and amount) to complement normal welding environments (Keats, 2011).
On the other hand, wet welding uses a system that allows a welder to weld an area that is in a wet environment (Amit, 2005). Here, the welder must wear protective gear (suitable for movement in water environments). Besides, the welder must use an electrode designed for under-water welding. The main advantage of wet welding over dry welding is affordability and ease of implementation. Although dry welding results in strong and correct welds, dry welding is both complex and expensive to carry out (Silva, 1971). As a result, wet welding is very common in under-sea welding.
Under-sea welding operates on a similar principle as ordinary welding. Here, a power supply located onshore connects to the weld through long wires. One terminal of the power source connects to the electrode while the other terminal connects to the metal body (Welding, 2012). A welder initiates an electric spark by placing the electrode in a momentary attachment with the metal body (Keats, 2011). The electric spark originates from a sustained effort by the electric current to jump the small gap between the electrodes and the metal body (Silva, 1971).
Meanwhile, the electric spark heats the metal body and melts the electrode (Keats, 2011). Therefore, the welder needs (to keep up the electrical spark) to make sure that the electrode is close enough to the metal body by making proper adjustments, which coincide with the rate at which the electrode melts (Stepath, 1973). Apart from melting the electrode, the electric spark heats a covering sheath on the outer surface of the special electrode (Keats, 2011). As a result, the electrode sheath releases a covering envelope around the weld area, which protects the weld (Amit, 2005).
Multiple risks can result from under-sea welding. Usually, the electric arc produced in water environments creates an electrolysis reaction, which results in the build-up of hydrogen and oxygen gases (American Welding Society, 2005). A combination of these two gases is highly explosive (Welding, 2012). Besides, welders can absorb high amounts of nitrogen gas on returning onshore; hence, a risk of nitrogen poisoning. Moreover, under-sea welders are at a greater risk of electrical shocks when compared with onshore welders (American Welding Society, 2005).
The risks and complexities that involve under-sea welding make it necessary for involved parties to take up a range of protective measures; hence, making the venture expensive. A dry under-sea weld (for a single weld) costs $100,000 on average (Amit, 2005). Multiple technologies promise to mitigate the above risks and improve the quality of under-sea welds (Lythall, 2000). The use of under-sea robots is an emerging approach in under-sea welding. Other promising technologies include friction and explosive welding (Welding, 2012).
Many offshore structures continue to emerge in the UAE. Oil exploration at offshore locations is leading to high numbers of offshore wells, which contribute a significant portion of the total oil and gas output in the UAE. In an effort to reduce their dependence on an oil economy, many states in the UAE, including Dubai, are diversifying their economy to include other sectors like tourism and commerce. As a result, a lot of offshore construction, including artificial islands, is ongoing.
A lot of under-water infrastructures (such as water pipes) is crucial to provide basic services there (Vijay, 2011). Moreover, the well-developed sea transport system in the UAE relies on thousands of offshore vessels, which can benefit from under-sea welding. On several occasions, offshore structures will fail; thus, prompting a need for appropriate repairs. Failure of an offshore structure could arise from piping leakages, or from any other malfunction, which affects the production potential of an offshore facility (Vijay, 2011).
There is always the question of when and why under-sea welding is better suited for offshore repairs. Here, one needs to look at the convenience of carrying out under-sea welding, instead of replacing, or moving malfunctioned parts to the surface for repair. Apart from providing convenience for offshore repairs, under-sea welding can save on the number of hours that would otherwise result from onshore welding (Stepath, 1973).
The loss of production time for critical offshore facilities, such as offshore wells (producing tens of thousands of oil barrels per day), will lead to adverse effects for the UAE economy; hence, making under-sea welding a more viable option in such situations. Moreover, it is cheaper to do under-water welding (for offshore facilities) as opposed to carrying out repairs onshore. Unsurprisingly, under-sea welding ranks among the most important professions in the UAE.
The emergence of multiple offshore structures in the UAE makes it necessary to explore under-sea welding as a viable option for onshore welding. Many companies prefer under-water welding in comparison with onshore welding, due to a package of benefits offered by under-water welding, especially the convenience to undertake repairs in shorter periods.
Companies that operate critical production facilities located offshore cannot afford to lose production time; hence, a need to use time-saving approaches, such as under-sea welding to repair malfunctioning devices. Although it requires high-quality training, may prove expensive at times, and needs special tools, under-water welding is more useful for several offshore repairs than onshore welding.
American Welding Society. (2005). Safety and Health Worksheet New York: American Welding Society Press
Amit, M. (2005) Underwater welding . Bombay: Indian Institute of Technology Press
Keats, D. (2011). Manual of wet welding New York: McMillan
Lythall, G, (2000) Dry Hyperbaric underwater welding New York: American Welding Institute Press
Silva, H., (1971) Underwater welding with iron – powder electrodes, Welding Journal , 7(2), 42-68
Stepath M. (1973). Underwater welding and cutting yields slowly to research, Welding Engineer , 11(4), 121-42
Vijay, V. (2011) Application of underwater welding processes for subsea pipelines. The Australian Pipeliner , p 24
Welding (2012)
- Building Consrtuction for Fire Protection
- Ethical Behaviour in the Engineering Workplace
- Workers Safety: Protecting Welders From the Hazards of Poisonous Gases and Other Dangers
- Whats Mean Robotics Welding
- Fabrication and Welding Project
- System Requirements Engineering in Complex Situations
- Components and Aspects of Whistleblowing in Engineering
- Model of Induction Motors
- Globalization Impacts on System’ Engineer Career
- Improving the Internal Combustion Engine Efficiency
- Chicago (A-D)
- Chicago (N-B)
IvyPanda. (2020, May 7). Welding Underwater - Engineering. https://ivypanda.com/essays/welding-underwater-engineering/
"Welding Underwater - Engineering." IvyPanda , 7 May 2020, ivypanda.com/essays/welding-underwater-engineering/.
IvyPanda . (2020) 'Welding Underwater - Engineering'. 7 May.
IvyPanda . 2020. "Welding Underwater - Engineering." May 7, 2020. https://ivypanda.com/essays/welding-underwater-engineering/.
1. IvyPanda . "Welding Underwater - Engineering." May 7, 2020. https://ivypanda.com/essays/welding-underwater-engineering/.
Bibliography
IvyPanda . "Welding Underwater - Engineering." May 7, 2020. https://ivypanda.com/essays/welding-underwater-engineering/.

STUDENT LOGIN
623.882.3483
- Commercial Divers International
Underwater Welding: The Intersection of Technology and Skill
Updated: Aug 20
Step into the realm of underwater welding, a field where toughness and precision collide, offering a demanding yet rewarding career for those who dare. This article cuts through the steel of underwater welding, from the hardcore training and certifications needed to the solid career opportunities that lie in the depths. Discover how Commercial Divers International (CDI) equips you with the ironclad skills required to thrive in this industrial battleground, where every spark underwater is a testament to durability and skill.
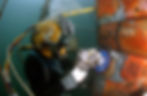
What is Underwater Welding?
Underwater welding is a specialized field that combines diving skills with welding expertise, allowing professionals to perform welding tasks beneath the water's surface. This challenging career requires not only a mastery of welding techniques but also certifications in commercial diving, ensuring that underwater welders are equipped to handle the unique environmental and safety challenges they face. As an intersection of technology and skill, underwater welding is pivotal in various industries, including marine construction and offshore oil and gas operations, where underwater welding equipment and advanced technology play crucial roles.
Path to Becoming an Underwater Welder
Aspiring professionals must first undergo rigorous training in both welding and commercial diving, acquiring essential certifications that affirm their expertise and adherence to safety standards. At Commercial Divers International, we offer comprehensive programs that equip students with the necessary skills and knowledge, from basic underwater welding techniques to advanced courses in underwater welding technology. Our curriculum is designed to meet industry demands, ensuring our graduates are well-prepared for the challenges and opportunities in this dynamic field. By choosing our school, students gain access to state-of-the-art underwater welding equipment and hands-on experience, setting a solid foundation for a successful career in underwater welding. If you're ready to dive into an exciting career that merges cutting-edge technology with critical skill, enroll at Commercial Divers International today and take the first step toward becoming a certified underwater welder .
Certifications for Diving and Welding
To pursue a career in underwater welding, individuals must obtain certifications in both commercial diving and welding. These certifications ensure that underwater welders are proficient in safe diving practices and skilled in various underwater welding techniques, meeting the industry's stringent standards for safety and expertise.
Essential Diving Certifications
The Association of Diving Contractors International (ADCI) establishes the industry-wide safety standards for commercial diving. Using skills learned from Commercial Divers International , graduates can expect to be thoroughly prepared for certificates in:
Entry-Level Tender
Focus on basic diving skills and underwater work knowledge.
Air Diver Certification
Essential for divers working with surface-supplied air, covering more advanced diving techniques and safety protocols.
Mixed-Gas Diver
For more advanced divers, this certification allows them to use mixed gasses for deeper and more complex dives, which is crucial for certain underwater welding jobs.
Saturation Diver
For divers who undertake very deep diving operations using saturation techniques, which are often required in complex underwater construction and welding tasks .
Skills and Techniques of Commercial Divers
Commercial divers possess a robust set of skills and techniques essential for performing complex tasks in challenging underwater environments. They are proficient in various diving methods, skilled in the use of sophisticated diving and welding equipment, and adept at executing repairs, inspections, and constructions under water. Furthermore, these divers are trained in emergency procedures and safety protocols, ensuring they can manage the unpredictable nature of underwater work efficiently and safely.
Technology in Underwater Welding
Underwater welding technology is a sophisticated field that utilizes advanced equipment and techniques to ensure precise and durable welds beneath the water's surface.

Kirby Morgan
To get divers in the water and equip them with the tools and technology necessary to succeed, our school utilizes Kirby Morgan Dive Systems International technology. Their equipment is designed and manufactured to be the highest quality underwater breathing equipment available, while maintaining a strong reputation for safety and excellent customer service.
Hyperbaric Diving Career Opportunities
Underwater welders have the unique advantage of engaging in diverse projects, from offshore oil rig maintenance to underwater infrastructure repair, providing a dynamic and rewarding career path. With the right training and certifications, such as those from Commercial Divers International, individuals can unlock lucrative positions in this niche industry , where demand for skilled professionals continues to grow.
What is the Advantage of Underwater Welding?
Cost savings.
Underwater welding can reduce the cost of removing a structure from the water and dry docking.
Underwater welding can reach parts of offshore structures that other methods can't.
Convenience
Underwater welding uses standard welding machines and equipment, and doesn't require enclosures.
People Also Ask
What new technology is being used underwater welding.
Laser-assisted metal flux-cored welding
Laser-based deep welding
Thermography and spectroscopy data
Why is Underwater Welding Interesting?
It's a challenging and rewarding career that involves unique skills and a variety of work environments. Underwater welders work in diverse settings, including shipyards, dams, offshore oil rigs, and underwater construction sites.
What is the Technical Term for Underwater Welding?
Hyperbaric welding, which involves welding at elevated pressures, typically underwater. It can also be done in a dry, pressurized enclosure, which is known as dry welding.
Best Commercial Diving Training School
A career in underwater welding is stepping into a world where grit meets precision, where every dive is a mission, and every weld contributes to the backbone of industries like oil, gas, and marine construction. At Commercial Divers International, we arm you with the robust skills, critical certifications, and real-world experience needed to excel in this tough, demanding profession. This isn't just a job; it's a call to those who are ready to take on the deep, tackle the elements, and secure structures that keep our world running. If you've got the mettle to forge a career in underwater welding, step up to the challenge at Commercial Divers International . Learn more about how our program can get you started on your own path.
- Getting Started
Recent Posts
Qualifications for a Career as a Commercial Diver
Trade Schools Accepting the GI Bill
How Much Can You Earn as an Underwater Welder?

IMAGES
COMMENTS
Free Essay: Underwater welding Underwater welding is a vary high risk job and can only be done for a certain amount of years about 10-15 years. This job...
Underwater Welding Essay. Decent Essays. 712 Words. 3 Pages. Open Document. Underwater welding is an exciting job for the person who likes the idea of diving thousands of feet, while being paid well.
The paper describes principles of underwater welding and recent trends in research works undertaken for enhance welding technology and properties of underwater welds.
There are two types of underwater welding: dry and wet welding (Vijay, 2011). Dry welding employs a chamber to seal the area that needs welding repair (Lythall, 2000). The chamber must have requisite components, such as oxygen (incorrect concentration and amount) to complement normal welding environments (Keats, 2011).
Part 1 of this paper covers developments in microstructural optimization and weld metal porosity control for UWW. Part 2 discusses the hydrogen pickup mechanism, weld cooling rate control, design, and qualifi-cation of consumables. It ends with a description of the advancements in FCAW applications for UWW.
Underwater welding is used in the repair of offshore structures and pipelines, ships, submarines, and nuclear reactors. Current techniques that are generally used are wet underwater welding and hyperbaric welding. The most commonly used wet welding technique is SMAW and FCAW including self-shielded FCAW (60).
Underwater welding is a specialized field that combines diving skills with welding expertise, allowing professionals to perform welding tasks beneath the water's surface.
In this literature study, offshore welding was investigated in three perspectives such as welding process environment, applicable materials for offshore environment and suitable modern welding technologies for underwater welding of offshore structures.
Essay On Underwater Welding Underwater welding is a vary high risk job and can only be done for a certain amount of years about 10-15 years. This job contains a lot of time away from home but it contains a lot of traveling.
Published 1 December 2008. Materials Science, Engineering. Underwater Welding - A Review The paper describes principles of underwater welding and recent trends in research works undertaken for enhance welding technology and properties of underwater welds.